Mazak CNC Machines
Mazak is one of the leading companies in CNC machining. They offer a wide array of commercial quality CNC machines that can do basically anything and everything imaginable. Their machines are designed for a variety of different industries.
Mazak offers multi-tasking CNC machines, 5 axis CNC machines, turning machines, Palletech machines, horizontal machines, vertical machines, and automated machines, not to mention control solutions. Basically, if you need one, they have the machine that can do it. They even have machines that can supply the machines with more products, either one more pallet or a hundred more pallets. Their systems can basically operate by themselves with the lights out, if need be.
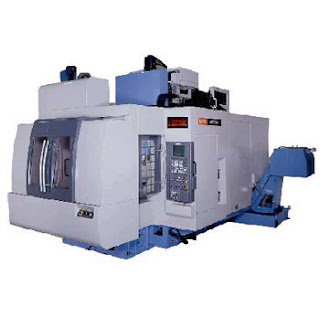
The multi-tasking Mazak CNC machines offer many different services such as drilling, tapping, milling, turning, boring and finishing all in the same set-up. This is what they call their Done-in-One machine. If your company is looking to be competitive, cost efficient and lean, then this is the perfect machine for you. This machine offers compressed lead times, no tolerance buildup, increase output, reduce part costs, and much more.
The 5 axis Mazak CNC machine offers both types of configurations that are typical of 5 axis machining. Positioning the work piece into different planes or variety of angles to the spindle or the continuous 5 axis cutting motion is what this machine is capable of. It will do both. With the advancement in technology, the affordability of the 5 axis CNC machines have improved and now many companies will only buy this particular machine for their business.
The Mazak turning center stresses productivity. This machine offers the shortest amount of time from set up to start up. Programming is basically fairly easy as many components are already built in, making this machine perfect for new comers. Built in parameters include: cutting speeds and feeds, tool management, tool path and checking 3D simulation.
Mazak CNC machines serve a variety of different industries which include: the aerospace industry, energy industry, medical industry, automotive industry, con/agra industry, contract manufacturing, and mass production. Their machines can be useful in all of these industries.
The Mazak CNC machines are well designed and can stand up to the test of time. They offer plenty of support for their product and can get your business set up like it needs to be to improve quality, efficiency and still be cost effective. If you are looking for the perfect CNC machine that can take your business to the next level, then Mazak is definitely the answer to your dreams.
If you have any further questions about Mazak CNC machines, visit their website. You will be able to find a variety of information about their different machines, customer support, their technology centers and the services that they have to offer. Contact them via telephone or email and they will be able to answer any questions that you may have. Depending upon what you need, they will be able to get you up and going with a Mazak CNC machine.
By Ivan Irons
Mazak is one of the leading companies in CNC machining. They offer a wide array of commercial quality CNC machines that can do basically anything and everything imaginable. Their machines are designed for a variety of different industries.
Mazak offers multi-tasking CNC machines, 5 axis CNC machines, turning machines, Palletech machines, horizontal machines, vertical machines, and automated machines, not to mention control solutions. Basically, if you need one, they have the machine that can do it. They even have machines that can supply the machines with more products, either one more pallet or a hundred more pallets. Their systems can basically operate by themselves with the lights out, if need be.
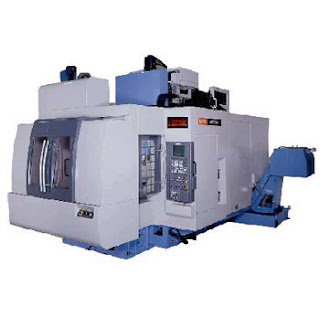
The multi-tasking Mazak CNC machines offer many different services such as drilling, tapping, milling, turning, boring and finishing all in the same set-up. This is what they call their Done-in-One machine. If your company is looking to be competitive, cost efficient and lean, then this is the perfect machine for you. This machine offers compressed lead times, no tolerance buildup, increase output, reduce part costs, and much more.
The 5 axis Mazak CNC machine offers both types of configurations that are typical of 5 axis machining. Positioning the work piece into different planes or variety of angles to the spindle or the continuous 5 axis cutting motion is what this machine is capable of. It will do both. With the advancement in technology, the affordability of the 5 axis CNC machines have improved and now many companies will only buy this particular machine for their business.
The Mazak turning center stresses productivity. This machine offers the shortest amount of time from set up to start up. Programming is basically fairly easy as many components are already built in, making this machine perfect for new comers. Built in parameters include: cutting speeds and feeds, tool management, tool path and checking 3D simulation.
Mazak CNC machines serve a variety of different industries which include: the aerospace industry, energy industry, medical industry, automotive industry, con/agra industry, contract manufacturing, and mass production. Their machines can be useful in all of these industries.
The Mazak CNC machines are well designed and can stand up to the test of time. They offer plenty of support for their product and can get your business set up like it needs to be to improve quality, efficiency and still be cost effective. If you are looking for the perfect CNC machine that can take your business to the next level, then Mazak is definitely the answer to your dreams.
If you have any further questions about Mazak CNC machines, visit their website. You will be able to find a variety of information about their different machines, customer support, their technology centers and the services that they have to offer. Contact them via telephone or email and they will be able to answer any questions that you may have. Depending upon what you need, they will be able to get you up and going with a Mazak CNC machine.
By Ivan Irons